PRE-SALE SERVICE
The company's product pre-sales technology, processing technology plan, and tooling design;
Technical document output after tooling design, tooling production, verification tracking, and improvement;
Preparation of product testing and customer processing procedures;
Technical services for product turnkey projects;
Carry out pre-sales and after-sales machine tool operation and programming training for customers;
Preliminary technical communication with customers, technical Q&A, plan production and review, completion of process analysis, layout drawing; formulation, and preliminary risk assessment based on the project;
Responsible for the customer's on-site fixture program;
Analysis and solutions of abnormal problems during commissioning at the customer site;
Customer site equipment commissioning and product trial cutting;
According to the customer's products and drawings, process beat accounting.
Pre-sale Service Procedures of
CNC Machining Center Manufacturer
The company's product pre-sales technology, processing technology plan and tooling design
Technical document output after tooling design, tooling production, verification tracking and improvement
Preparation of product testing and customer processing procedures
Technical service for product turnkey project
Carry out pre-sales and after-sales machine tool operation and programming training for customers
Preliminary technical communication with customers, technical Q&A, plan production and review, completion of process analysis, layout drawing formulation, and preliminary risk assessment based on the project
Responsible for the customer's on-site fixture program
Analysis and solutions of abnormal problems during commissioning at the customer site
Customer site equipment commissioning and product trial cutting
According to the customer's products and drawings, process beat accounting
Cases of CNC Machining Center
Pre-sale Case
Nissan 600 sets of 117/118 bearing seat production line plan
1. Production guidelines:
600 sets/day (117/118 bearing seat)
2. Requirements of the processing line:
1) CNC machining center suitable for automatic production line;
2) Hydraulic tooling fixture;
3) Automatic loading and unloading device and conveying device;
4) The overall processing technology and processing rhythm.
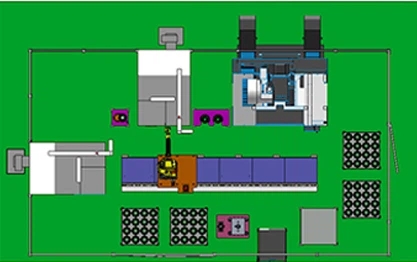

Production Line Case Introduction
The automatic production line storage equipment of this scheme is stacked trays (the
quantity of each tray needs to be negotiated with the customer), and the workpiece
in the tray is fixed
It will be determined after providing 3D drawings or real objects of the workpiece
blanks.
1. The worker puts the rough-machined parts into the material tray (as shown in the
figure), and forks to the designated position by the forklift;
2. After the forklift replaces the material tray, manually press the button to
confirm;
3. The robot grabs the workpiece for loading work.
Robot Walking Axis Introduction
This structure adopts joint robot, servo motor drive, rack, and pinion transmission, etc., which makes the robot perform linear motion back and forth; realizes the function of one robot serving multiple machine tools and multi-station grabbing workpieces, which can increase the working coverage of the joint robot;
The walking track adopts a steel pipe welded base, a servo motor, and a rack and pinion drive mode to increase the working coverage of the joint robot and effectively improve the utilization rate of the robot;
The walking track is installed on the ground.
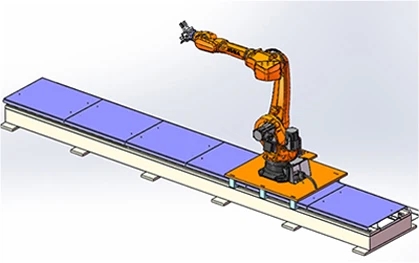
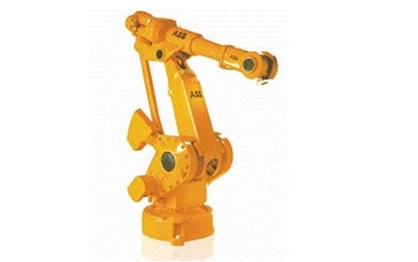
ABB robot: IRB-4400-60
It has a wide range of motion including the back and bottom of the robot and can be mounted on a ceiling-mounted model. Because the lateral width of the robot is reduced to the limit, it can be installed close to adjacent robots, fixtures, or workpieces. High-speed movement from the standby position to the working position, as well as rapid positioning during short-distance movement.
Robot Clapboard Gripping Mechanism
1. According to the characteristics of the part, we adopt the three-jaw external support method for loading and unloading, which can quickly realize the U-turn of the part in the machine tool;
2. The mechanism is equipped with a position detection sensor and a pressure sensor to detect the clamping status of the parts and whether the pressure is normal;
3. The mechanism is equipped with a pressure maintaining device, and the workpiece will not fall off in a short time when the power is cut off and the main gas circuit is cut off; 4. Using a hand-changing device, by replacing the gripping mechanism, the gripping of different materials can be completed quickly.
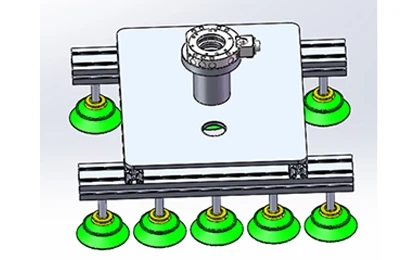

The Precise Hand Changing Device
The precise hand changing device is used to quickly change the gripper, tool end, and other actuators of the manipulator. Reduce production idle time and improve the flexibility of the robot. Its characteristics:
1. Unlock and tighten by air pressure;
2. Various power, liquid, and gas modules can be used;
3. The standard configuration can be quickly connected to the gas source;
4. Special insurance agencies prevent the risk of accidental air loss;
5. There is no spring reaction force;
6. Applicable to the field of automation.